Alles im Griff – auch in der Krise
Dräger produziert eine der in der Pandemie gefragtesten Waren auf dem Weltmarkt: Beatmungsgeräte. Regierungschefs und Staatsoberhäupter meldeten sich sogar persönlich, um Lieferungen bestellen. Um dem Bedarf wenigstens annähernd zu decken, musste die erst 2017 eröffnete „Zukunftsfabrik“ in Lübeck ihre Produktionskapazitäten in Rekordschnelle massiv um das Vierfache erweitern. Einblick in eine unternehmerische Jahrhundertaufgabe des Familienunternehmens.
„Der größte Feind der Qualität ist die Hektik“, sagt Stephan Schick (42), Leiter der Auftragsabwicklung des Geschäftsbereichs Therapie bei Dräger. „Wenn es hektisch wird, unterlaufen zwangsläufig Fehler.“ Und die dürfen nirgends weniger passieren als beim Bau lebensrettender Technik. Deshalb sahen Leute wie Schick es als eine ihrer entscheidenden Aufgaben, den Produktionsteams in Ausnahmesituationen wie der Pandemie ein entgegengesetztes Klima zu bieten: „Unsere Mannschaft muss physisch und mental gesund bleiben, dementsprechend strahlen wir genau das als Führungskräfte auch aus – um zu signalisieren, dass wir die Prozesse im Blick haben und Entscheidungen wohlüberlegt treffen.“
Mensch, Maschine und Material für die massive Produktionserweiterung ertüchtigt
Dazu befähigt, trotz mancher Anspannung, die typisch hanseatische Leidenschaft, die auch Dräger groß gemacht hat. Natürlich verfolgte man in Lübeck das Weltgeschehen zum Coronavirus ganz genau; auch hier haben sich die Bilder überlasteter Kliniken eingebrannt. Stephan Kruse, Leiter des Geschäftsbereichs Therapie, versucht, diese so gut es geht von sich fernzuhalten: „Auf diese Emotionalität darf ich mich nicht einlassen, sonst kann ich keine schnellen Entscheidungen treffen, wie sie seit Beginn der Pandemie dringend benötigt wurden.“ Schnell entscheiden musste der 50-Jährige bereits ab Tag eins der Krise. Es galt, die drei großen „M’s“ in kürzester Zeit für eine massive Produktionserweiterung zu ertüchtigen: Mensch, Maschine und Material.

Von da an vermehrte sich auch die Anzahl der Produktionsmitarbeiter – bis zu 300 neue Stellen wurden kurzfristig am Standort geschaffen. Der in Deutschland häufig beklagte Fachkräftemangel war dabei – situationsbedingt – kein Thema. Die neuen Mitarbeiter kamen auch aus Unternehmen anderer Branchen, die Personal freisetzen mussten. Mit der Einarbeitung soll der Hochdruck-Betrieb in der Revalstraße nicht ausgebremst werden: „Im Elektronik-Gebäude in unserer Firmenzentrale in der Moislinger Allee haben wir deshalb eine Trainingswerkstatt errichtet. Hier wurden neue Mitarbeiter geschult, um sich anschließend in die Produktivität in den Produktionshallen in der Revalstraße einbringen zu können.“
„Milk Run“ half bei der Jahrhundertanstrengung
Das zweite „M“, die Maschinen, standen von Anfang an unter einem guten Stern. In den neuen Produktionshallen wurde bereits vieles auf potenzielle Steigerungsraten sowie maximale Flexibilität gedacht und ausgelegt – die bestehenden Kapazitäten waren Ende 2019 gerade mal zu 75 Prozent ausgelastet. Somit war es auch nicht nötig, in größerem Umfang neue Produktionslinien zu errichten, oder gar das Rad neu zu erfinden. Das digital gesteuerte Hochregallager hält indes die bis zu 800 Bauteile und Komponenten eines Beatmungsgeräts bereit.
Beim „Milk Run“, einer Art fahrplangetaktetem Zugbetrieb, werden sie just in time an die einzelnen Montagelinien gebracht. Das entsprechende Test-Equipment sorgt für die Funktionsprüfung der fertiggestellten Einheiten. Die sensiblen Prüfgeräte mussten ebenso aufgestockt werden, damit jederzeit genügend verfügbar sind. Nach bestimmten Laufzeiten benötigen sie Abkühlphasen, um fehlerfreie Messungen zu gewährleisten. Zudem hat eine Restrukturierung im vergangenen Jahr den Unternehmensbereich Medizintechnik neu ausgerichtet. Auch das half bei der Jahrhundertanstrengung dieser Tage.
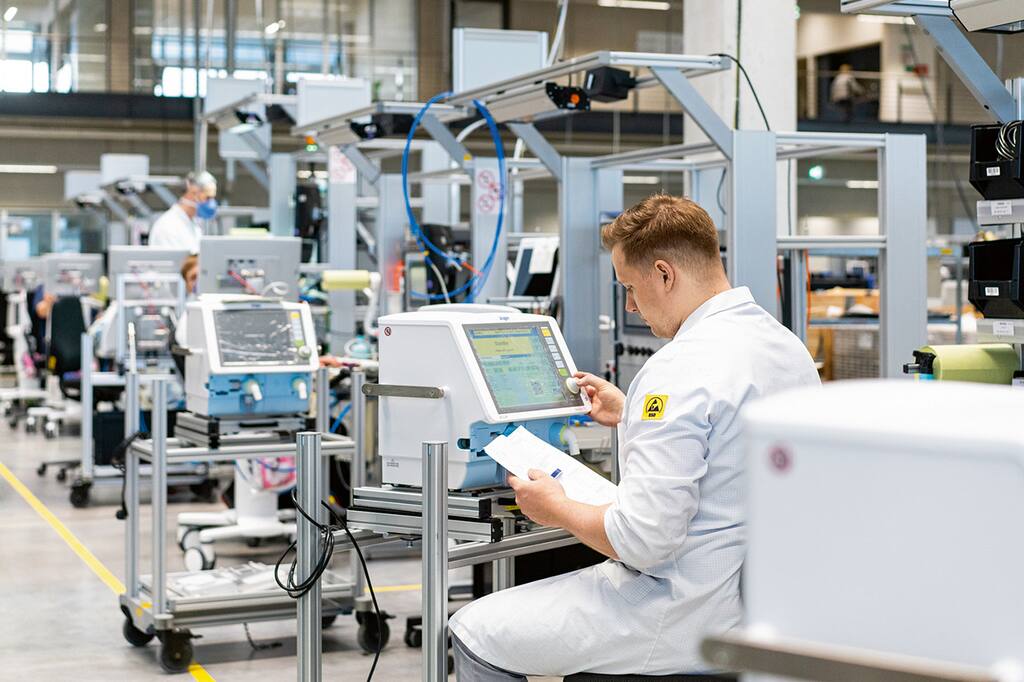
Gefahr fragiler Lieferketten
Aus der Restrukturierung ist ein neuer Bereich hervorgegangen: „Customer Order Execution“ (kurz COE) – von der Materialbeschaffung, -vereinnahmung und -lagerung, über die verschiedenen Produktionslinien bis zum Order-Management und Versand befindet sich nun die Bearbeitung von Kundenaufträgen in einer Hand. Hierfür ziehen die Beteiligten an einem Strang. „Das bringt einige Vorteile und ist ein Grund dafür, weshalb wir schon bis Ende März 2020 eine Verdopplung der Produktion geschafft hatten“, bilanziert Stephan Schick.
Doch niemand sollte glauben, man wäre allein durch diese Umorganisation vor bösen Überraschungen gefeit. Das zeigt sich am dritten „M“, dem Material. Die einzelnen Komponenten der Beatmungsgeräte werden von Herstellern aus aller Welt geliefert, die ihre Kapazitäten ebenfalls deutlich ausweiten mussten. Falls dadurch eine der fragilen Lieferketten überdehnt und sich Versorgungslücken auftun, lässt sich für manche Komponente nicht mal eben ein zweiter Hersteller aus dem Hut zaubern. Doch der lange Weg vom Auftragseingang bis zur Auslieferung der Geräte war für den Bereichsleiter Produktionslogistik, André Sieber (40), bislang kein Stoff für Albträume: „Nach 20 Jahren Berufserfahrung ist es zwar ein sehr herausforderndes Szenario, aber es hat mich noch keine schlaflose Nacht gekostet, weil die gesamte Kette tatsächlich gut funktioniert.“
“Jeder von uns will helfen!“
Wenn dann wieder eine erwartete Sendung von Beatmungsgeräten „Made in Lübeck“ irgendwo auf der Welt in einer Klinik oder einem improvisierten Not-Lazarett eintrifft, endet die Reise für Dräger damit nicht. „Unser Angebot ist sehr viel breiter als die eigentliche Lieferung der Geräte“, sagt Bereichsleiter Kruse. Es umfasse auch flankierende Schulungsmaßnahmen, etwa für Anwender, die gerade erst als Gesundheitshelfer rekrutiert wurden: „Wir stellen zudem eigene Websites und Trainingsvideos zur Verfügung, denn wir müssen leider davon ausgehen, dass es in manchen Kliniken nicht immer nur hoch qualifiziertes Personal zur Bedienung der Geräte geben wird.“
Bis zum Ende des größten Gesundheitsnotstands, den die Welt im 21. Jahrhundert bisher gesehen hat, wird die Revalstraße noch viele Monate ohne Unterbrechung Beatmungsgeräte (Evita V800, Savina, Oxylog 3000 plus u. a.) und Anästhesiegeräte (Atlan, Perseus u. a.) ausstoßen. Dass dies gelingt, liegt vor allem auch am „Bodenpersonal“, den Kolleginnen und Kollegen auf dem Shop Floor – wie Tobias Germann: Der 40-jährige Monteur, seit 2012 im Unternehmen, spürt wie seine Kolleginnen und Kollegen die besondere Verantwortung, gerade auch für die am stärksten von dem Virus heimgesuchten Länder: „Von uns würde niemand sagen: Was gehen mich Italien, Spanien, Großbritannien, die USA oder andere an? Nein, jeder von uns will helfen!“ Nach einer kurzen Pause fügt er hinzu: „Wenn ich an der Stelle eines COVID-19-Patienten wäre, der dringend eine künstliche Beatmung bräuchte, würde ich mir auch wünschen, dass anderswo Menschen alles dafür tun, um mehr Geräte zu produzieren.“
Sie sehen gerade einen Platzhalterinhalt von YouTube. Um auf den eigentlichen Inhalt zuzugreifen, klicken Sie auf die Schaltfläche unten. Bitte beachten Sie, dass dabei Daten an Drittanbieter weitergegeben werden.
Erfahren Sie hier mehr zum Wirtschaftspreis Innovator des Jahres.
In dieser extrem ungewissen Zeit hat sich mal wieder gezeigt, dass alle Mitarbeiter bei Dräger, sich als “eine große Familie” sehen.
Und das verbindet unglaublich – nur gemeinsam ist man stark!!!