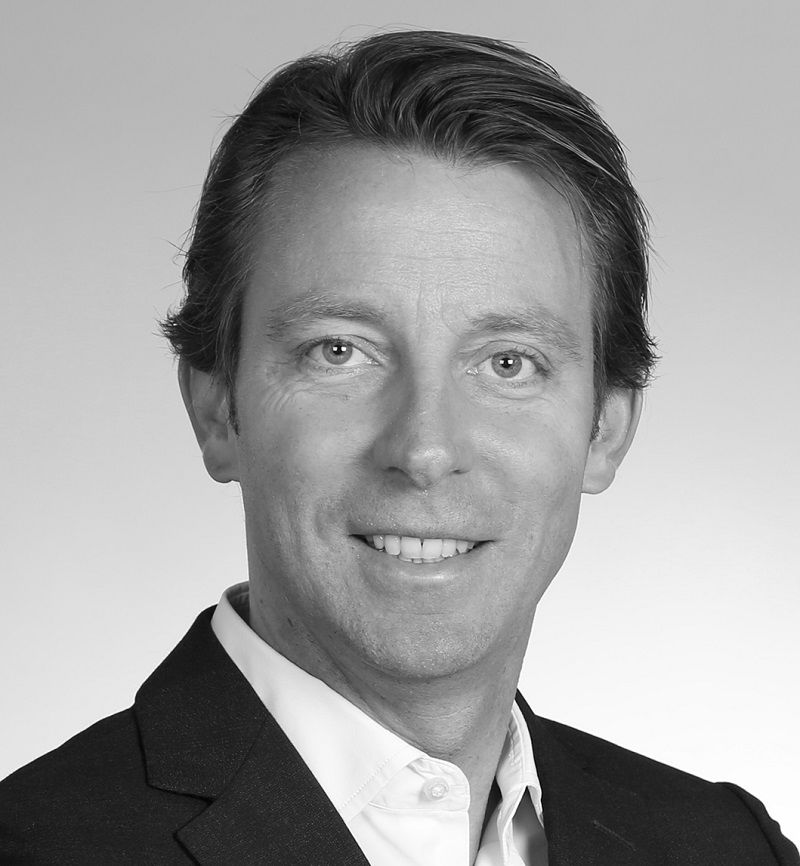
Aluminium’s bright future is in cast plates
The trend away from steel to aluminium continues. Aluminium cast plates and aluminium components are becoming increasingly important as a basis for semi-finished products. There are solid arguments for both developments, not only with regard to costs. Further innovations will reinforce this trend around the world. Written by Dr. Philip Grothe, CEO alimex GmbH Precision in aluminium
Companies around the world, regardless of the industry, are under enormous cost and time pressure. The preference for ever higher material requirements and more innovative material solutions, which are required by designers, users and end consumers, plays a decisive role here.
For materials, aluminium is the driving force that satisfies many of these preferences. To name just one industry, automobiles today contain three times more aluminium than those built 20 years ago. The demand for aluminium is on the rise throughout the world, because there is an increasing number of areas of application in which the benefits can be maximised.
As a leading innovator in cast plate processing for many years now, we have been able to secure a significant share in this development. This makes us quite proud. Even more importantly, we can now turn our attention to the future: Our innovations, which we have developed out of our practical experience with our customers, and our great efforts in research and testing have shown that the widespread success enjoyed by aluminium has by no means come to an end. On the contrary: The market is only just beginning to take off.
Aluminium is increasingly replacing steel
The reasons behind the sharp rise worldwide in the use of aluminium are varied. One of the driving global megatrends for this development is certainly that of climate change, which calls for more light-weight structures, long-lasting products and more recycling facilities, to reduce energy consumption. In this respect, aluminium has many advantages over steel. This gives it an edge in the transport sector, in the construction of vehicles, aeroplanes and in the rail sector.
But without aluminium’s special properties, the increasingly rapid innovation cycles in our world would be unthinkable in many fields, such as electrical engineering, the building industry or machine construction. Aluminium makes product and technological innovations possible, from semiconductors to kitchen appliances, and from photovoltaic systems to sport bikes. Not to mention the megatrend towards new consumer habits that favour the increasing use of aluminium in packaging.
More specifically and in business practice in the metal processing industry, it is, however, the tangible efficiency and cost benefits in particular that make aluminium more often than not the material of choice. And these can be improved even further by using cast plates as the starting basis for production.
More about the author:
https://die-deutsche-wirtschaft.de/dr-philip-grothe/
Cast plates versus roll-bonded plates
Today, a wide variety of aluminium alloys are used in fields in which mainly steel or stainless steel was used in the past. The ever greater demands placed on these aluminium alloys must not, however, drive costs up. While aluminium roll-bonded plate alloys have mainly been used to this end in the past, there is now a trend towards aluminium cast plates.
The manufacture of alimex cast plates, which we developed more than 35 years ago, has established itself as the process of choice throughout the world and has transformed a wide variety of applications of roll-bonded plates from the 5000, 6000 and 7000 series. Applications can be found in the electronics, laser, packaging and optical industries, in the medical devices industry and laboratory technology, and in display panels, semiconductors and photovoltaic systems. They all benefit from the excellent dimensional stability for sensitive, high-quality and attractive intended applications and the savings that come from eliminating deformation, reduced waste, faster processing times and the prevention of additional annealing.
Solutions from experience and research
Indeed, we will be able to improve the fields of application and so the benefits relating to costs and efficiency even further. Since the process development of the cast plates, the search for such solutions has led to the ‘corporate DNA’ of alimex. Our corporate policy ‘Innovation through investment’ sums this up.
We put great emphasis here on intensive partnerships with our suppliers, on collaborative research projects such as those with the RWTH Aachen university – one of the leading technical universities worldwide – and a regular exchange of information with the Fraunhofer Institute for Chemical Technology and the equally famous Jülich Research Centre. The aim is to develop new applications at the forefront of scientific research.
Above all, though, it is the proximity to the end customers that, together with our specialist dealers and wholesalers, gives us valuable insight into the behaviour and applications of cast plates in practice and so important empirical experience. To the entire Group this means increased emphasis on cooperation with our customers with their subsidiaries in the United Kingdom, the Netherlands and the US. We will now also institutionalise this important input with a partner advisory board as an innovation platform.
This year, specific services have arisen from this, such as subcontracting, measurements and tests of chemical compositions, and macroscopic and microscopic evaluations.
The result of all these efforts is reflected in our innovations and thus in the benefit to our customers. For some segments, these efficiency and cost benefits should show up in new products.
Multiple cost benefits in mould construction and plastics processing
Moulds such as, in particular, low-pressure moulds, moulds arising from thermoforming and prototypes moulds, but also tools propagated from our ‘Hot seller’ ACP 5080 (R) have been manufactured for many years now. The ACP 5080 series is characterised by the near absence of internal stress, excellent machining properties and relatively high strength properties. Parts of thicknesses of up to 1060 mm, widths of up to 2800 mm and lengths of up to 6000 mm are standard in this series.
This enables very high cutting speeds in the machining of aluminium. Component processing times can be cut by more than 40 percent over steel, for example. The expenses for machine tools are also significantly reduced due to weight reductions. In addition, tool wear in the aluminium machining is three to four times lower than in the machining of steel.
Furthermore, moulds made of aluminium have a much better thermal conductivity than steel moulds, which in turn considerably reduces the cycle times in the production of plastic parts, leading to further costs savings.
Here, we are considered an innovative cast plate expert and will bring further developments to the market. A unique ACP cast plate from the 7000 series whose strength properties will exceed the strength values of all cast plates currently available on the market will soon be launched.
The 7000 series is predestined in particular for blow moulding and for moulds that require a high load. The planned tensile strength of >400 MPa is sufficient for almost all requirements of this kind. This innovation, called ACP 7, is characterised by a unique and extremely high yield strength with an value expected to be around 375 MPa. This is extremely interesting for applications in injection moulds. Excellent polishing properties in conjunction with very good dimensional stability and excellent machinability offer a low-cost alternative in this extremely profitable industry.
Innovations for machine construction and precision plates
The ACP 5080 precision plate is used mostly in machinery and system construction. This cast plate both originating from the 5083 alloy and milled on both sides is characterised by an optimal flatness, a very narrow yet constant thickness tolerance, and a consistently clean milled surface with a roughness of <0.3 mu.
Customers working in the fields of printing-, tobacco- and packaging machines as well as automation systems prefer this alimex cast plate due to these core properties. The aesthetic demand, for example, in terms of an anodised finish, has increased enormously in these industries.
In light of this aesthetic aspect, alimex is planning on bringing to the market in the second quarter a further innovation, the product Eloxpure®. It will be available in two variants for highly demanding visible parts, firstly in 5754 ACP Eloxpure® and secondly in ACP 5080 Eloxpure®. With these products, alimex provides its customers with a complete solution with regard to highly demanding, anodised precision plates.
Semiconductor industry/Vacuum technology
The use of our high-precision cast plates is extremely widespread in this business segment. No other competitor has so much know-how and experience in this extremely demanding market segment. alimex has been known for its quality with ACP 5080 ‘S’ and ‘RS’ in the field of high vacuum applications in the solar and semiconductor industries for years. The decisive improvement of the ultrafine cast structure has been achieved as a result of the specially developed casting process, further treatment processes and a reduction in the microporosity.
Here too, we will be able to offer users further improvements in the near future. Later this year, the products ACP 5080 LPQ® and ACP 5754 LPQ® will be brought to market. These will reduce the microporosity in the pore level by a further 25 percent and provide additional optimisation opportunities and cost reductions for highly demanding and highly sensitive applications, such as process chambers.
Bright prospects
Both our cast plates and cast cuttings and our complex components manufactured in different alloys have won wide acceptance in markets worldwide. The benefits of aluminium as a whole, the casting products in particular, and our new product offerings in specific cases will spawn an unwavering interest in the material. As mentioned above: The market is only just beginning to take off.
Dr. Philip Grothe is CEO of alimex GmbH Precision in aluminium
Schreibe einen Kommentar