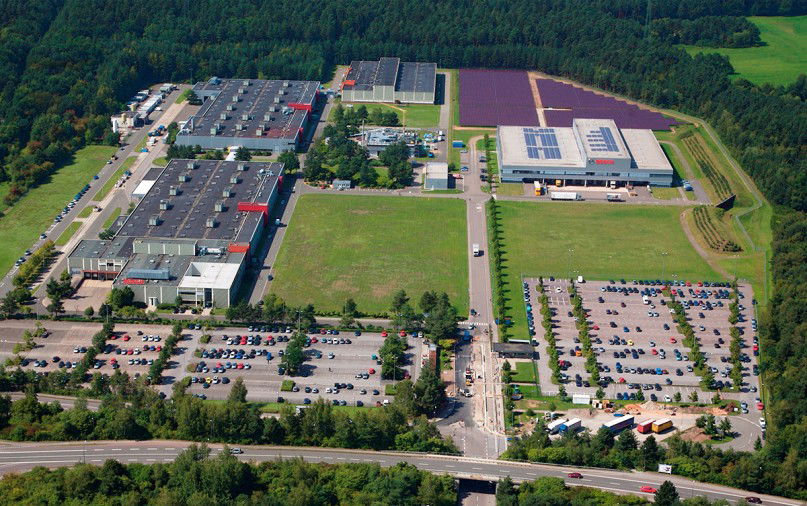
Best–Practice Energieeffizienz: 25 Prozent weniger Energie im Werk Homburg
Mit dem Ziel den Energiebedarf ganzheitlich zu senken und Energiekosten einzusparen, entschied sich Bosch am Standort Homburg für die Einführung eines ganzheitlichen Energie- und Ressourcenmanagements. Die gesamte Optimierung der Reinigungsanlagen brachte eine Senkung des anlagenspezifischen Energiebedarfs von rund 25 Prozent – im Vergleich entspricht das dem Bedarf von 1.400 Einfamilienhäusern.
Vor allem in produzierenden Unternehmen wird Energie zu einem der wichtigsten Wettbewerbsfaktoren im globalen Streben nach Kostenvorteilen und Marktanteilen. Energieeffizienz kann die Attraktivität nach innen und außen steigern und somit die Wettbewerbs- und Konkurrenzfähigkeit erhöhen. Am Bosch-Standort Homburg wird rund 75 Prozent der erforderlichen Energie alleine in der Fertigung benötigt. 5.400 Mitarbeiter produzieren hier unter anderem moderne, kraftstoffsparende und umweltschonende Hochdruckeinspritzsysteme für Dieselmotoren. Seit 2007 wird der gesamte Produktionsprozess energetisch optimiert und so ausgerichtet, dass der Energiebedarf unter Beibehaltung der hohen Qualitätsstandards größtmöglich reduziert wird.
Systematische Vorgehensweise bringt Erfolg
Auf Basis von Analysen, Optimierungen und Kontrollen werden organisatorische Maßnahmen durchgeführt sowie Investitionen für die Optimierung der Anlagen getätigt. Bis heute konnte dadurch der Energiebedarf des gesamten Standorts um16 Prozent reduziert werden. Und auch die Umwelt profitiert – rund 20 Prozent des Klimagases Kohlenstoffdioxid wurden bisher in Homburg hierdurch vermieden. Für die Identifikation möglicher Stellhebel zur Senkung des Energiebedarfs in der Produktion wurde der sogenannte ‚Energiewertstrom’ entwickelt. Diese Methodik schafft die erforderliche Transparenz über die Energieverbräuche von Anlagen, Arbeitsschritten bis hin zu Verbräuchen und Energiekosten einzelner Produkte. Auf Basis der Ergebnisse wurden Bestandsanlagen, Produktionsschritte und anschließend der gesamte Produktionsprozess energetisch optimiert.
Bestandsanlagen bergen hohe Einsparpotenziale
Eine hieraus resultierende Maßnahme in der Homburger Fertigung war die energetische Verbesserung von mehr als 150 Reinigungsanlagen, auf die circa 15 Prozent des gesamten Energieverbrauchs des Standorts fallen. Sie dienen der Reinigung der in Homburg gefertigten Komponenten für Dieseleinspritzsysteme von Spänen, Emulsionen oder Ölen. Um das Energieeinsparpotenzial der Reinigungsanlagen auszuschöpfen wurde systematisch nach dem Motto „korrigieren, organisieren und vorbeugen“ vorgegangen. „Ähnlich der Wertstromanalyse analysieren wir die einzelnen Arbeitsschritte der Maschine hinsichtlich Energiearten, Temperaturen, Volumenströme sowie Betriebsparametern. Erst dann ist es möglich, Einsparmöglichkeiten zu identifizieren und Schritt für Schritt zu optimieren“, sagt Stefan Regert, Bosch-Projektleiter Energiemanagement am Standort Homburg.
Die gesamthafte Optimierung der Reinigungsanlagen brachte eine Senkung des anlagenspezifischen Energiebedarfs von rund 25 Prozent – im Vergleich entspricht das dem Bedarf von 1.400 Einfamilienhäusern. Alleine die Absenkung der Badtemperatur um wenige Grad Celsius brachte eine enorme Reduktion des Energiebedarfs. Auf das Reinigungsergebnis hatte diese Einzelmaßnahme keine negativen Auswirkungen, was auch von der Qualitätssicherung bestätigt wurde. Die energetische Betrachtung und Optimierung von Bestandsanlagen birgt für produzierende Unternehmen enorme Einsparpotenziale. „Wir haben nach unserer Methodik insgesamt 450 Bestandsmaschinen in Homburg optimiert. Die durchschnittliche Verbrauchssenkung pendelt nach unseren Erfahrungen zwischen 10 und 20 Prozent, je nachdem um welche Maschinenkategorie es sich handelt“, so Stefan Regert, Projektleiter Bosch Werk Homburg.
Abschaltmanagements schafft Reduktion der Grundlast um 75 Prozent
Hohe Einsparungen brachte auch die Einführung eines Abschaltmanagements. Im ersten Schritt wurden die energetischen Verbrauchsdaten der Maschinen im Produktionsprozess analysiert und die Risiken bewertet. Im zweiten Schritt wurde festgelegt, wie die Maschinen zielgerichtet und damit bedarfsorientiert vom Netz genommen werden können. Zur Erfolgskontrolle werden eigens entwickelte Energieberichte eingesetzt, die eine Verfolgung und Absicherung der Nachhaltigkeit ermöglichen.
Durch das gezielte Abschaltmanagement konnte der Energiebedarf in der Grundlast um durchschnittlich 75 Prozent reduziert werden. Sofern Investitionen erforderlich waren, amortisierten sich diese in kürzester Zeit. „Am Wochenende und nach Schichtbetrieb werden die Maschinen von den Mitarbeitern abgeschaltet und gehen somit vom Netz. Die Mitarbeiter wurden im Vorfeld geschult. Zusätzlich befindet sich an jeder Maschine eine sogenannte Energiesparkarte“. erläutert Projektleiter Stefan Regert die tägliche Handhabung.
Mindestens genauso wichtig wie die Optimierung bestehender Anlagen ist jedoch auch die vorbeugende Arbeit. Für die Beschaffung neuer Maschinen wird am Standort ein Energiepflichtenheft eingesetzt. Das Heft definiert verbindliche Energieeffizienzkriterien, die der Anschaffung neuer Anlagen berücksichtigt werden müssen. Energiefresser kommen somit erst gar nicht mehr in die Werkshallen. Die Übertragung dieser Erkenntnisse in den Beschaffungsprozess schließt den Regelkreis bei den Bestandsanlagen.
Das langjährige Know-how bei der Steigerung der Energieeffizienz in der Produktion und der Dienstleistungs- und Produktexpertise im Bereich Energie gibt Bosch auch an andere produzierende Unternehmen weiter. Michael Blichmann, Geschäftsführer der Bosch Energy and Building Solutions GmbH, plädiert für den ganzheitlichen Ansatz: „Um wirklich alle Potenziale heben zu können, müssen technologische und prozessuale Verbesserungen mit Zielen und Strategien des Unternehmens einhergehen und dann konsequent und nachhaltig umgesetzt werden. Erst dann ist es möglich, das Thema ‚Energieeffizienz’ dauerhaft als Wettbewerbsvorteil zu nutzen.“ Bei unseren Projekten dreht sich alles um die Frage, was getan werden muss, um das Thema Energie dauerhaft als Wettbewerbsvorteil auszurichten“, so Blichmann weiter. Vier Kernaspekte stehen dabei im Vordergrund: a) die Umwandlung fixer in variable Energiekosten, b) die Reduktion großer Energiekostenblöcke, c) die Erhöhung der Versorgungssicherheit und d) die Steigerung des Green Images. Die Erfahrungen von Bosch in Energieeffizienzprojekten mit produzierenden Unternehmen zeigen kurze Amortisationszeigen und schnelle, aber dauerhafte Erfolge.
Am Bosch-Standort Homburg werden rund 75 Prozent der erforderlichen Energie alleine in der Fertigung benötigt. 5.400 Mitarbeiter produzieren hier unter anderem moderne, kraftstoffsparende und umweltschonende Hochdruckeinspritzsysteme für Dieselmotoren. Bosch Homburg hat Reinigungsanlagen in der Fertigung von Dieseleinspritzkomponenten energetisch optimiert. Mit ihrem systematischen Ansatz konnten die Experten den Energieverbrauch der Reinigungsanlagen um rund 25 Prozent senken. Das entspricht dem Bedarf von 1 400 Einfamilienhäusern. Die Energiekosten konnten um etwa 25 Prozent reduziert werden.
Lesen Sie auch: Energieeffizienz als Management-Thema
Bosch Energy and Building Solutions GmbH
Mittlerer Pfad 4
70499 Stuttgart
Tel.: +49 711 811 – 261 15
www.bosch-energy.de
info.energy@de.bosch.com
Bilder: Bosch
Schreibe einen Kommentar