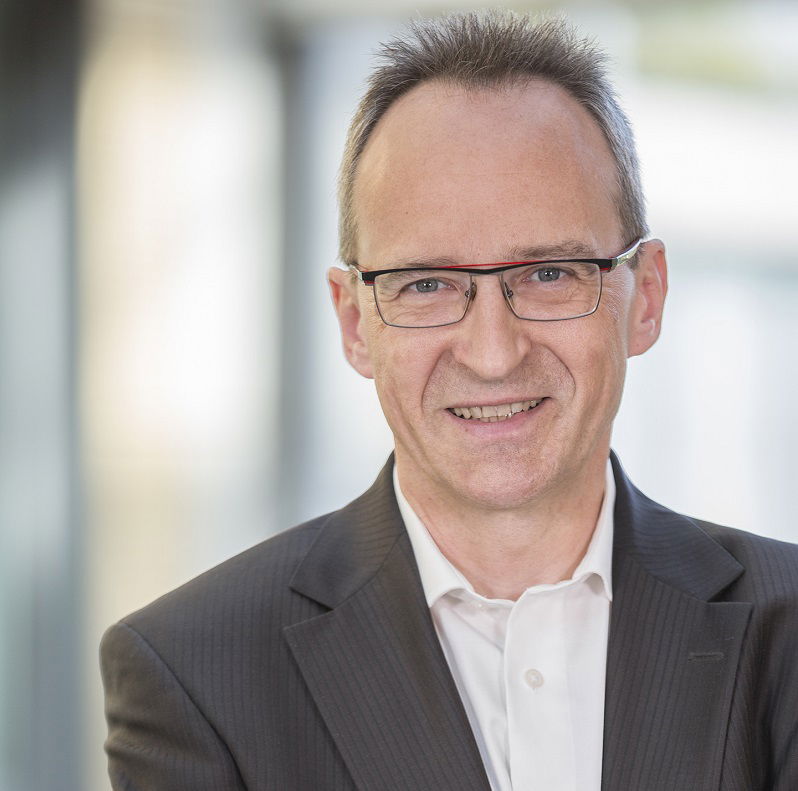
Klebetechnologien revolutionieren den Leichtbau
Klebstoffe sind echte Revolutionäre. Zumindest, was den Leichtbau angeht. Denn zukünftig werden immer mehr Verbindungen geklebt statt geschweißt oder genietet. Für die Industrie spart das Gewicht und Emissionen und beschleunigt sogar Arbeitsprozesse. Von Rüdiger Frisch, Technischer Leiter für Leichtbaulösungen Westeuropa bei 3M in Neuss.
Unser Konzern hat beispielsweise gerade einen neuen Klebstoff zur Marktreife gebracht, der ohne Vorreinigung auf öligem Untergrund aufgetragen werden kann. Das Öl wird einfach vom Klebstoff absorbiert. Der Hersteller spart sich also das Entfetten von Bauteilen, bei deren Produktion zum Verformen Öl genutzt wird. Gleichzeitig ist eine solche Methode auch ein Beitrag zum Arbeitsschutz, weil künftig keine Lösemittel zur Reinigung benötigt werden.
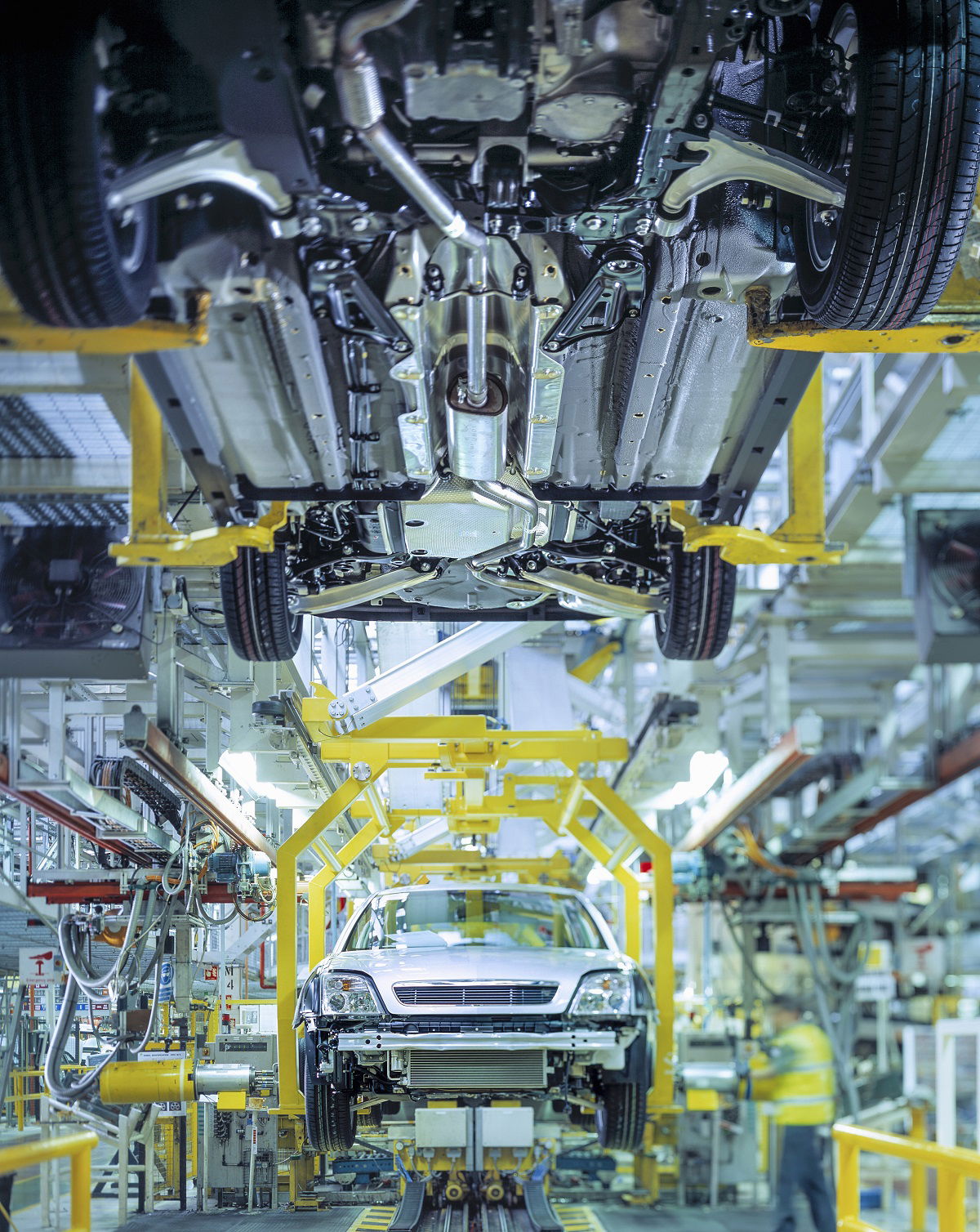
Kleben im Leichtbau reduziert außerdem Material und damit Abfälle. Ein neuartiger Klebstoff von 3M für die Luftfahrtindustrie befestigt Verschlüsse und Klammern an der Außenwand eines Flugzeuges. Bislang war dafür eine zusätzliche Fixierung notwendig, bis der Klebstoff ausgehärtet war. Das braucht Zeit – und die Fixierung wurde anschließend weggeworfen. Der neuartige Klebstoff sorgt dafür, dass die Verschlüsse sofort sicher sitzen.
Bedeutung von Klebetechnologien steigt
Viele Hersteller und Zulieferer setzen bereits seit mehr als 30 Jahren auf Lösungen von 3M. Klebebänder dienen beispielsweise zur Befestigung von Bauteilen am Fahrzeug, etwa in Spoilern, Radkasten-Verbreiterungen, Seiten-Beplankungen, Antennen oder Türdichtungen. Neuartige Lösungen werden immer dann wichtig, wenn Materialien mit eineinder verbunden werden, die sich nicht einfach bohren oder schweißen lassen. Und weil der Anteil an Leichtbaumaterialien in der Industrie steigt, nimmt auch die Bedeutung von Klebetechnologien zu. Ob Luftfahrt, Schienenverkehr oder Aufzüge: Überall dort, wo es um bewegte Massen geht, spielt die Gewichtseinsparung eine große Rolle.
15 Liter Klebstoff pro PKW
Das gilt insbesondere für den Autobau – dort zählt jedes Gramm. Schließlich stehen Autohersteller weltweit zunehmend unter Druck, umweltfreundlichere Fahrzeuge zu produzieren. Je weniger ein Fahrzeug wiegt, desto geringer ist der CO2-Ausstoß. Der Innovationszyklus wird dabei immer kürzer, der Materialmix nimmt zu. Um die unterschiedlichen Werkstoffe möglichst gewichtssparend zu verbinden, hat der Trend zum Kleben deutlich an Fahrt aufgenommen. Schon jetzt befinden sich durchschnittlich bis zu 15 Liter Klebstoff in einem PKW, Tendenz steigend.
Comeback von Metall
Wie groß der Bedarf an unterschiedlichen Klebelösungen ist, zeigt ein neuer Trend in der Automobilindustrie: Bis vor wenigen Jahren galten im Autobau noch Faserverbundwerkstoffe als Material der Zukunft. In der Zwischenzeit ist der Hype um Carbon & Co. etwas abgeklungen. Konnten sich die Experten noch vor zwei Jahren in einer VDI-Umfrage keinen Zuwachs von Metallen in der Serienproduktion vorstellen, stehen nun neuartige Aluminium-Magnesium-Legierungen im Fokus der Hersteller. Diese sind deutlich leichter und formbarer als vor einigen Jahren. Zum Einsatz kommen die neuen Materialien in Motoren, Karosserie oder dem Fahrwerk.
Auch diese werden zunehmend verklebt, denn Nieten oder Schweißen würde das Material schwächen und die Korrosionsgefahr erhöhen. Dazu sind bei 3M gerade Klebstofffilme in der Entwicklung. Sie kommen von der Rolle und lassen sich sehr gleichmäßig und sauber applizieren. In der Luftfahrt werden sie bereits länger eingesetzt, im Automobilbereich wurde inzwischen eine erste Serienanwendung realisiert.
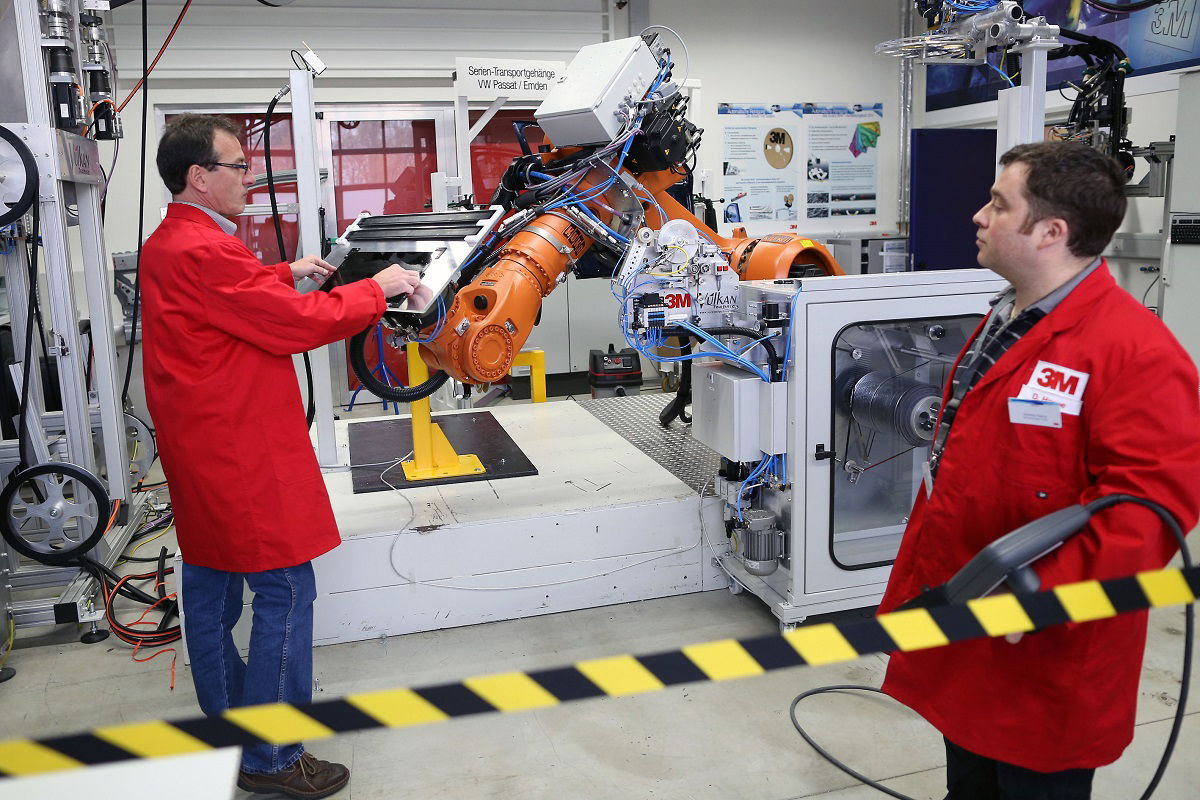
Serienmäßig genutzte Leichtbaulösungen von 3M
Auch 3M entwickelt immer wieder neue Leichtbaumaterialien. Aktuellstes Beispiel: 3M hat mit zwei Partnerunternehmen ein Füllmaterial entwickelt, mit dem sich das Gewicht der Heckschürze eines Sportwagens um 23 Prozent gegenüber dem Vorgängermodell reduzieren lässt.Der Verbundstoff findet sich serienmäßig auch in Armaturenbrettern oder im Unterbodenschutz von Kraftfahrzeugen wieder und sorgt für eine hohe Stabilität der Bauteile.Ein großer Automobilhersteller von Hybridfahrzeugen setzt einen innovativen Kantenschutz ein, der bis zu drei Kilogramm pro Auto einspart. Und ein neu entwickelter Vliesstoff hält nicht nur Fahrgeräusche ab, sondern spart 50 Prozent Gewicht im Vergleich zu herkömmlichen Materialien. Positiver Nebeneffekt: die Akustikabsorber können nicht schimmeln.
Gewichtsreduktion bis zu 180 Kilogramm je PKW
Aktuell arbeitet 3M unter anderem daran, das Gewicht von Sonnendächern in Autos zu reduzieren. Zudem ist geplant, die Eigenschaften des Glases so zu verbessern, dass sich der Wagen bei viel Sonne nicht so schnell aufheizt und Autofahrer ihre Klimaanlagen länger ausgeschaltet lassen können.Insgesamt können Autohersteller bereits heute mit den Leichtbau- und Klebelösungen von 3M bis zu 180 Kilogramm je Fahrzeug sparen. Das bedeutet eine Verringerung des CO2-Ausstoßes um knapp 22 Gramm pro Kilometer.Was sich zunächst nach wenig anhört, ist auf ein Autoleben bezogen eine Einsparung von mehreren Tonnen CO2.
Rüdiger Frisch ist technischer Leiter für Leichtbaulösungen Westeuropa bei 3M in Neuss. Der Multitechnologiekonzern erforscht und entwickelt zukunfts-weisende Technologien und Leichtbaulösungen für zahlreiche Industriebereiche in enger Abstimmung und Zusammenarbeit mit seinen Kunden. Klebetechnik ist eine der Kernkompetenzen von 3M. Allein in Deutschland arbeiten 80 Forscher und Anwendungstechniker in diesem Bereich.
Schreibe einen Kommentar